Wind Turbine Monitoring System
Using Acoustic Wave (Acoustic Emission)
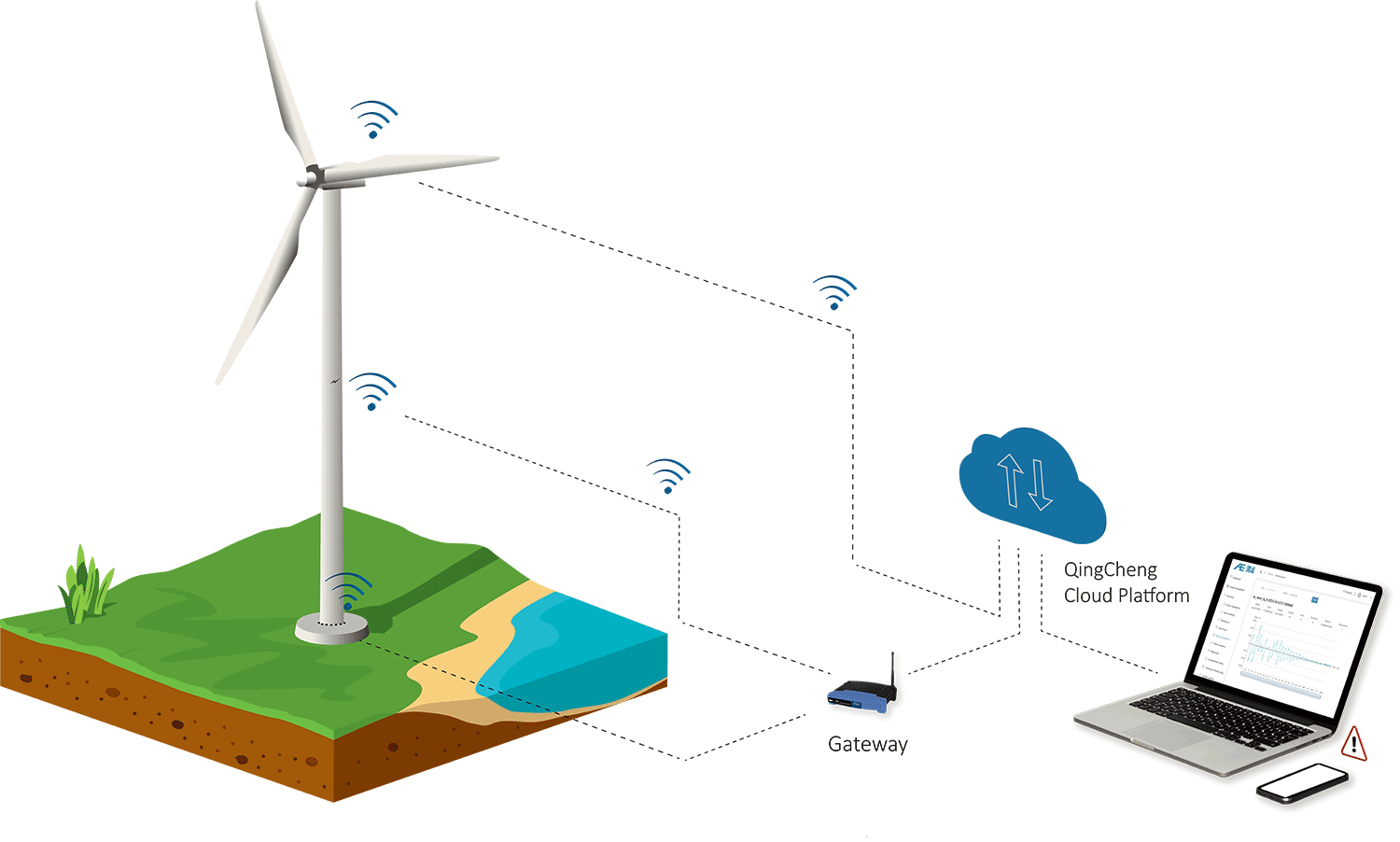
- System
- Communication
- Data Analysis
- Case Study
Condition based monitoring and maintenance is a key and effective means to decrease the huge downtime and repairing costs for wind power assets and systems. Compared to other NDT methods or vibration monitoring, acoustic wave (acoustic emission) monitoring has the advantages of dynamic monitoring during operation without any shutdowns and sensitive detection of earlier failing stage signals than vibration.
The system is suitable for wind turbine monitoring of various sections:
■ Structural Health Monitoring of
- Blades
- Main tower
- Grounding bolts
■ Condition Monitoring of
- Rotating bearing
- Gear box
Products for Wind Turbine Detection & Monitoring
RAEM1
RAEM1 is the IoT-AE wireless single channel monitoring system.
- Wireless communication wired power supply
- Signal triggering and 24/7 working
- Remote control and configuration
- Suitable for the transient signals such as cracking
- Position: Bolts, adjacent to flanges and the monitoring parts of the inner tower cylinder.
- Qty: Multiple
- Principle: Weak acoustic waves are often generated in the damage process of wind tower and the bolts, such as deformation, cracking, crack propagation and looseness of the bolts. The system receives and analyzes these acoustic waves to evaluate the health state of the tower and bolts.
RAEM2
RAEM2 is the IoT-AE wireless all-in-one monitoring system.
- Sensor, processor, communication and battery built-in, ready to use
- Time triggering and power saving for long term usage
- Wireless remote automatic operations
- Suitable for unattended leakage monitoring
- Position: Suitable positions on the rotating machines.
- Qty: Multiple
- Principle: The wear, pits, cracks, poor lubrication and other faults of the rotating machines lead to characteristic acoustic signals. The system collects and analyzes the acoustic signals regularly to obtain fault information and get the damage status of the rotating equipment.
RAEM1-6
Multi-channel testing or monitoring system
- Multiple sensors networking to locate the accurate defect’s locations
- Suitable for precise localization for cracking testing or monitoring
- Position: Inside the blades.
- Qty: Multiple (close to blade root)
- Principle: The system continuously monitors the acoustic signals generated by significant damage processes such as blade debonding, fiber fracture and crack growth, and evaluates the health of the blades.
System Connection and Communication
A variety of data output communication modes (Wi-Fi, 4G, LoRa, RS485, etc.) are available for selection, according to users’ requirements in order to achieve the regular testing, or the local long-term monitoring detection, or the remote long-term monitoring detection, or other application purposes.
*Choose the appropriate communication method according to the local conditions
Four Data Communication Methods:
1) Onsite operation and display:
2) Control room operation and display
3) Remote network direct communication system
4) Remote networking communication system:
Note: The above systems have the mobile phone app with Bluetooth communication functions for patrol inspection and field debugging settings.
Display & Analysis
The QingCheng IoT Cloud Platform, along with Alibaba Cloud, AWS, and other platforms, can be used as the data terminal for display, storage, and analysis. Below are the features of the QingCheng IoT Cloud Platform as examples:
- Real-time AE parameters and waveform displays
- Remote control and configure the devices
- Historical data storage and downloads
- Remote system firmware upgrade
- Parameter values rating to trigger alarm notifications for abnormal activities
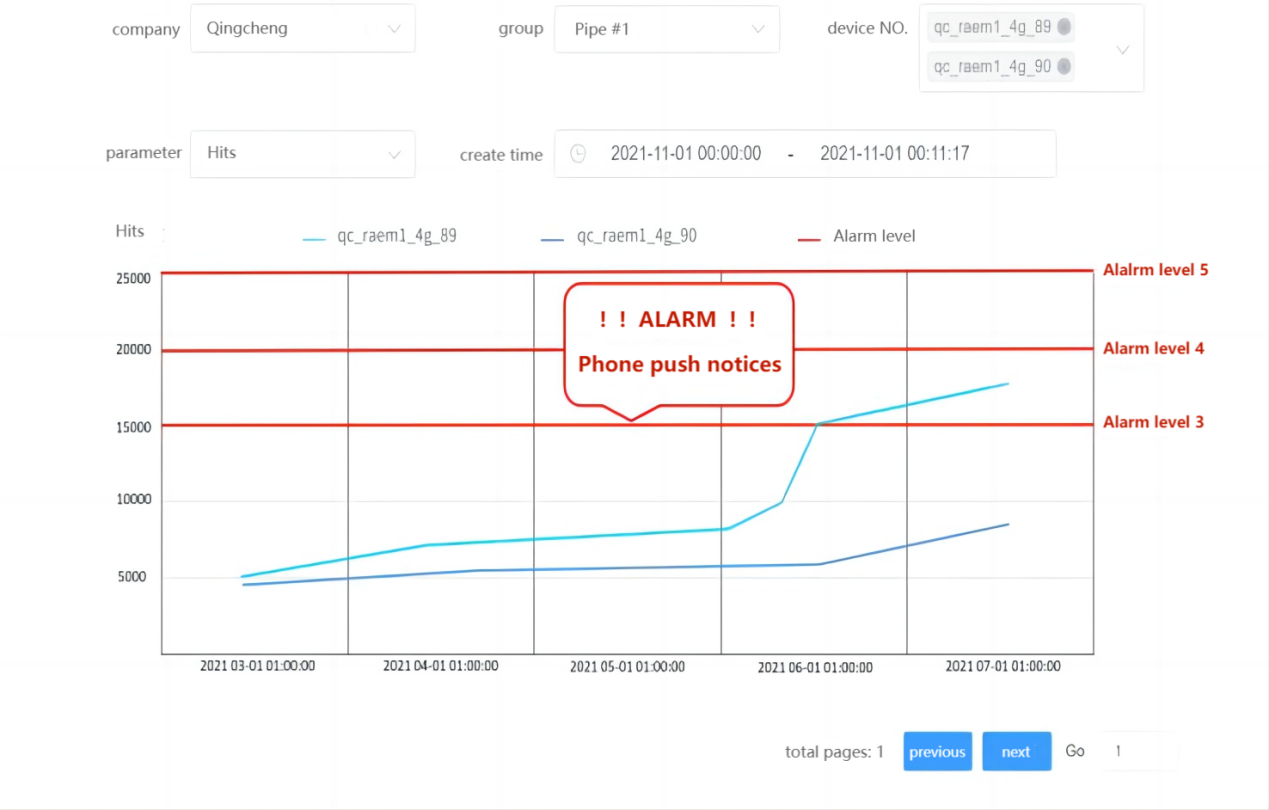
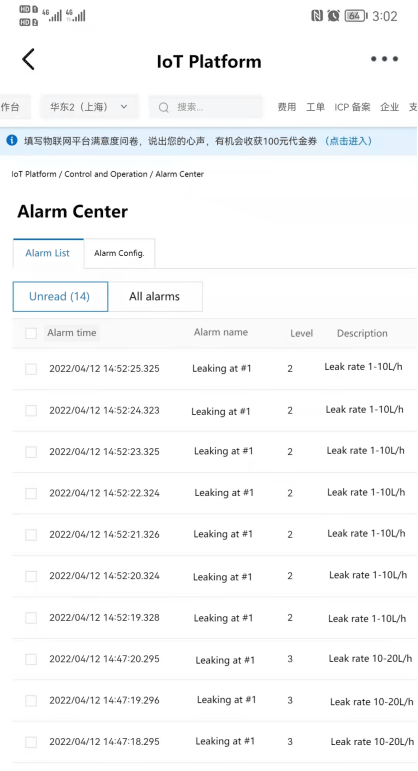
2) SWAE software for RAEM1/RAEM1-6
The RAEM1 or RAEM1-6 system can use the SWAE analysis software to analyze the real-time data and also for post data analysis.
- Various views and analytical functions, location analysis, correlation graph analysis, waveform analysis, Fast Fourier Transform, wavelet transform and more;
- Data storage and exportable to other formats for third party analysis.
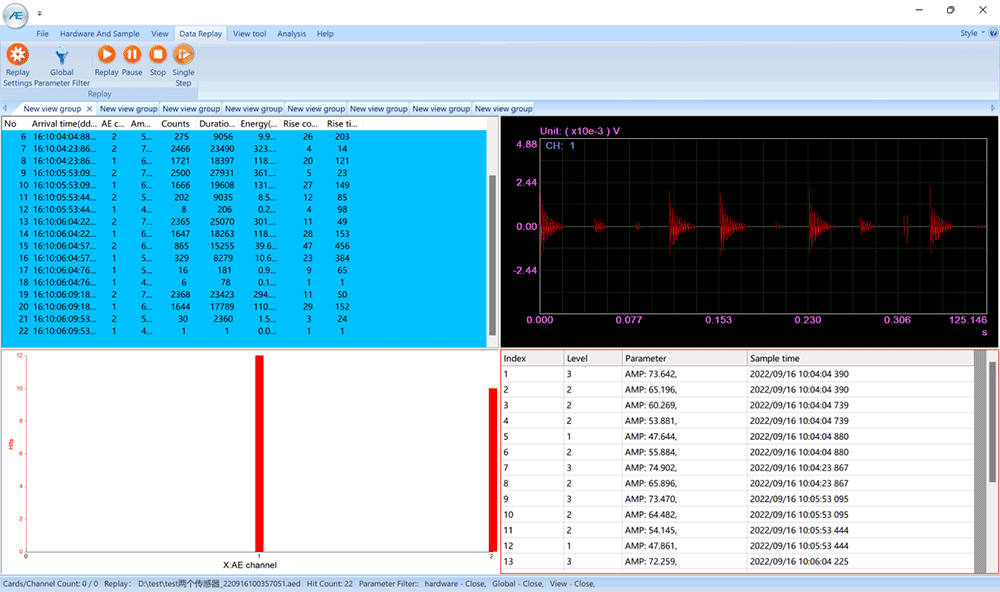
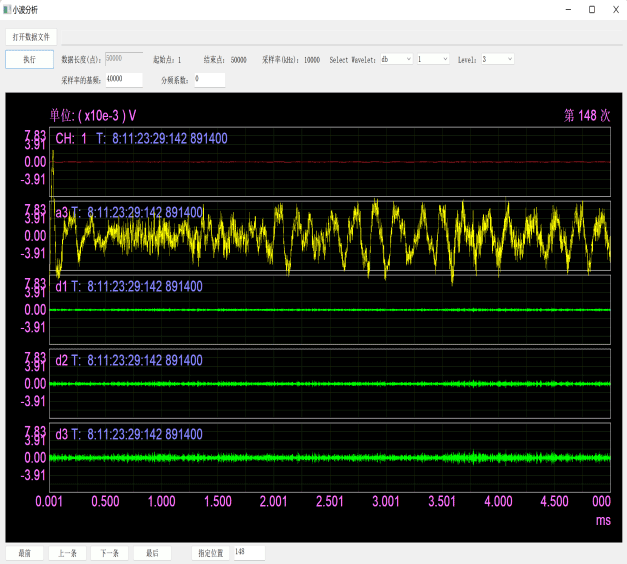
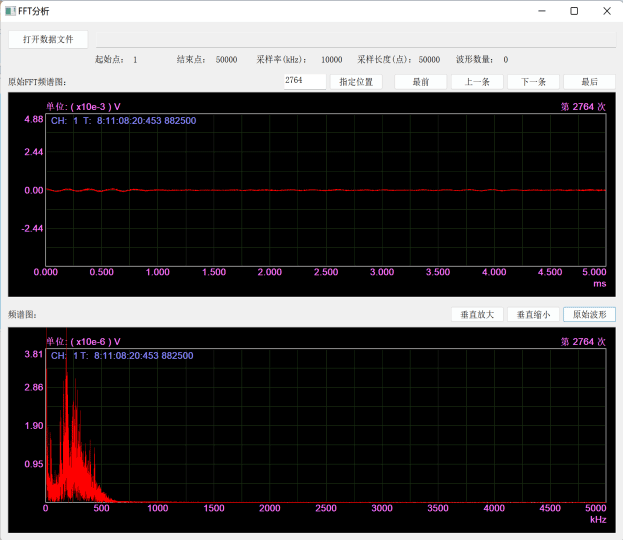
3) Smartphone App using Bluetooth for RAEM2
- Real-time parameters and waveform display
- Historical waveform and parameter query (parameters are amplitude, average signal level (ASL), energy, RMS; the display time accuracy is in minutes)
- Device control and configurations
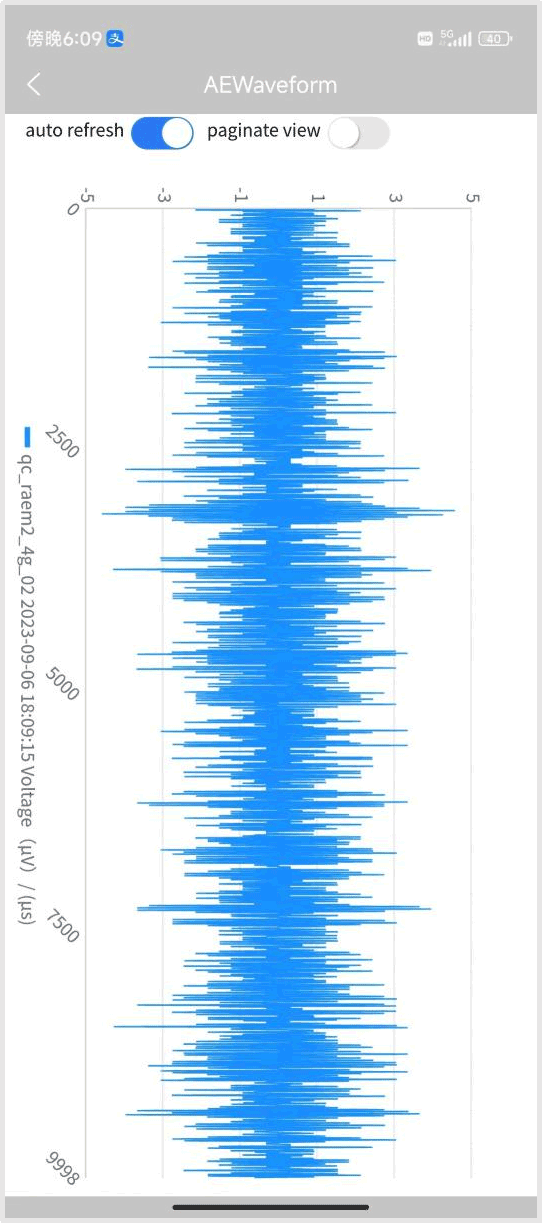
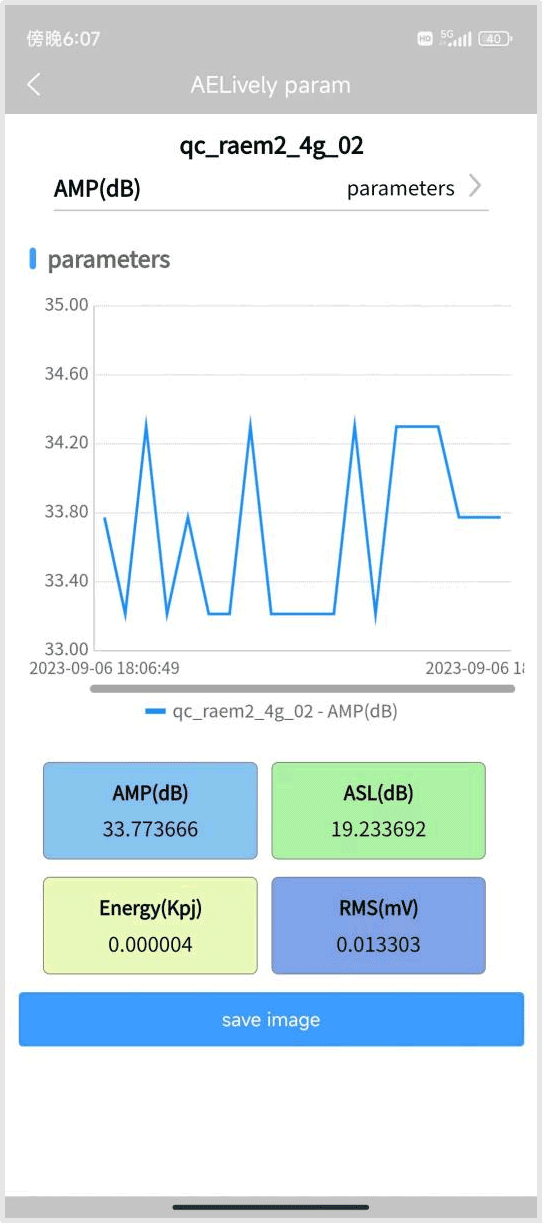
Contact Form
Please complete the form below to request your quote. We will be in contact as soon as possible.